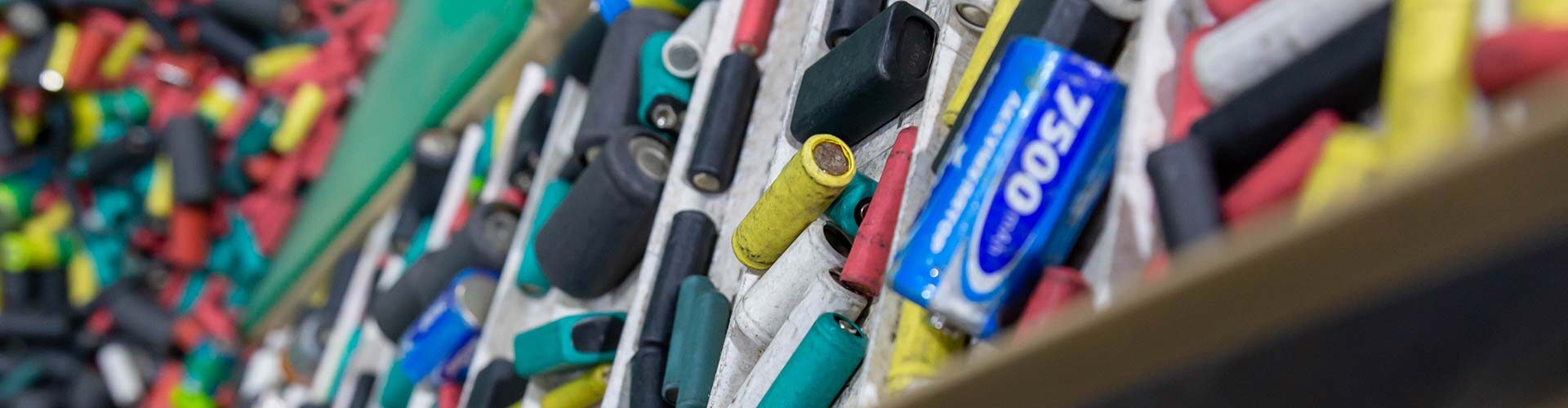
Reinventing Battery Sorting: Technology, Impact, and Innovation
The explosive growth of consumer electronics, e-mobility, and energy storage has triggered an unprecedented surge in battery usage. While this evolution empowers our daily lives, it also exposes a growing environmental and operational dilemma: how to efficiently and safely recycle the millions of batteries discarded each year.
Portable batteries are particularly problematic. These small but hazardous items often end up in mixed waste streams. Inside, they contain heavy metals like cadmium, lead, mercury, and reactive lithium compounds, which, if not properly managed, can contaminate soil, poison water systems, and trigger thermal events such as fires and explosions at recycling facilities. According to Waste360, the cost of lithium-ion battery fires to the waste and recycling industry is estimated at over $1.2 billion annually.[source]
This challenge is further amplified by product diversity. There are over 200 battery chemistries and form factors in circulation—from AAAA alkaline cells to high-capacity Li-ion 21700 units. Identifying, sorting, and processing this heterogeneous mix with both accuracy and safety is critical to advancing global sustainability goals.
The Real Cost of Inaccurate Sorting
Battery recyclers face enormous technical and economic pressure. Misclassified batteries can destroy processing equipment, compromise material purity, or spark chain-reaction fires. Improper separation also makes it harder to recover valuable metals like cobalt, nickel, and silver—many of which are already in short global supply.
Industry data suggests that recycling mixed batteries costs up to four times more than processing clean, single-chemistry streams. Yet, collection containers worldwide—whether in public spaces or facilities—typically gather unsorted waste. Effective, automated classification is not optional. It’s essential for financial viability, environmental safety, and compliance with extended producer responsibility (EPR) regulations.

Conventional Sorting Technologies: Capable, but Constrained
Several sorting technologies have been deployed to handle used batteries. Each has specific use cases, yet each carries limitations when applied to modern, mixed waste streams:
- Manual sorting is labor-intensive, slow, and subject to fatigue and human error. It’s also a health hazard for workers exposed to dust, corrosive materials, and the risk of thermal incidents.
- Optical systems rely on barcode scanning, label recognition, or color segmentation. These methods fail when labels are scratched, counterfeit, missing, or ambiguous. They also struggle with black plastic casings and multilayer wrappers.
- Magnetic sorting can only isolate ferrous from non-ferrous metals, which is useful in scrap processing but insufficient for distinguishing chemistries like NiMH and Li-ion.
- Weight-based or density-based methods may differentiate small formats (e.g., AA vs 18650), but they cannot accurately determine internal composition, especially among similar-sized chemistries.
These systems provide partial solutions. But none offer a reliable, chemistry-based approach that works across all battery types, including damaged or counterfeit units. That’s where X-ray technology redefines what’s possible.
The Scientific Backbone: X-ray Imaging and Material Discrimination
X-ray technology leverages the interaction of high-energy photons with matter. When X-rays pass through an object, different materials absorb them to varying degrees depending on atomic number, thickness, and density. This principle forms the basis of computed tomography and radiographic scanning used in security, medical diagnostics, and now—battery inspection.
In battery sorting, this approach reveals the internal structure of each cell: its electrodes, electrolyte type, canister thickness, and internal configuration. These parameters create a “radiographic fingerprint” that is unique to the chemistry (e.g., NiCd vs NiMH), allowing for accurate identification regardless of label condition.
When combined with artificial intelligence, the system continuously learns from new samples and builds a database of internal patterns. It can flag anomalies such as counterfeit units or hybrid compositions—critical for regulatory compliance and safety management.

X-ray Sorting in Action: From Analysis to Automation
The X-ray battery sorting process begins with debris removal, eliminating dust, broken pieces, and microcells. Batteries are then aligned and conveyed through the scanning zone, where high-speed detectors capture internal images. These images are interpreted by a neural network classifier, assigning a category based on chemistry.
Once categorized, each battery is sorted via pneumatic ejectors into designated containers. Unrecognized or damaged batteries are automatically sent to a fallback bin, preventing system blockage or contamination of clean streams.
The system operates with full operator shielding and complies with radiation safety standards (<0.3 µSv/h). It supports sorting of all common cylindrical formats, including AAAA, AA, C, D, 9V, 18650, and 21700.
LINEV Systems: From Innovation to Real-World Deployment
Since 2017, LINEV Systems has pioneered the use of X-ray imaging for battery analysis. The BATTERAY system, developed in-house, integrates proprietary algorithms and radiographic techniques into a turnkey sorting solution trusted across Europe.
Unlike traditional optical systems, BATTERAY “sees through” the battery, classifying it based on its actual chemical structure. It offers over 99.5% sorting purity for Alkaline and Zinc–Carbon cells, and over 95% for lithium-based and nickel-based chemistries. Its software also allows users to expand the sorting database with custom chemistries and sizes.
By combining machine vision, modular hardware, and scalable AI infrastructure, BATTERAY turns a complex environmental challenge into a streamlined, intelligent recycling process. It reduces manual labor, minimizes risk, and recovers value from every cell that passes through.
Conclusion: Technology for a Cleaner Planet
X-ray battery sorting is more than a technology—it’s a critical enabler of the circular economy. It addresses the urgent need for smarter waste handling while offering clear financial, operational, and environmental benefits.
As the world moves toward electrification and sustainability, innovations like BATTERAY ensure that battery recycling keeps pace—with intelligence, precision, and care for the planet.