The growing consumption of portable batteries has led to a global issue regarding their proper disposal and recycling. As a result, there is an increasing public focus on the correct method of collection, storage, and sorting of waste, as well as the development and modernization of recycling options to minimize the amount of recycled waste that may contain harmful substances. This is critical to preventing these substances from entering the soil, water, atmosphere, and human bodies.
Recycling has been made successful, in part, by lead-acid batteries, with over 97 percent of them being recycled in the USA today. This process is straightforward, and up to 70 percent of the battery’s weight can be reused as lead. Recycling is responsible for providing over 50 percent of the lead supply, and its primary aim is to prevent dangerous materials from ending up in landfills while also repurposing the extracted components to make new products.
Though batteries containing harmful substances will continue to be present, using them is not an issue as long as they are properly disposed of. Each battery type necessitates a distinct recycling process, which starts by sorting them into the appropriate categories.
Certain batteries and accumulators possess high concentrations of costly metals such as silver, nickel, cadmium, or zinc that exceed those found in natural ores. The production of batteries and accumulators is on a continual rise. As a result, collecting, categorizing, and recycling these products is vital to prevent hazardous heavy metals from entering the environment through household waste. It is also sensible to use raw materials from used batteries or accumulators in the metallurgical industry.
To effectively reuse valuable metals and substances in the industry, it is crucial to have a high degree of purity in the recycled battery sample, which is ideally over 95%. This is why sorting old batteries and accumulators by their electrolyte type is necessary after they have been collected in containers. Since 2017 our team has researched the possibility of using X-ray technology to solve the problem of identifying and sorting various types of used batteries. As a result, the X-ray system for sorting portable batteries, BATTERAY, was developed and manufactured. The BATTERAY, X-Ray Battery Testing system is a powerful and versatile tool for detecting the types of batteries.
LINEV Systems Has The Solution
By implementing our technology at the sorting stage, we can increase the overall efficiency of the recycling process by increasing the number of recycled batteries and reducing the cost of recycling. This will reduce the cost of all stages of the recycling process. Furthermore, the quality of the final product of processing is directly related to the quality of sorting. Different types of batteries yield different fractions of substances with various fields of application. Heavy metals in fertilizers can defeat their agricultural purpose, while impurities in metals can make the metallurgical processing process more difficult. It is also essential to note that higher sorting purity dramatically reduces the risk of emergencies such as explosions and fires in lithium battery recycling plants.
The LINEV Group has been conducting research since 2018 to investigate the feasibility of using X-ray technology to identify and sort various types of used batteries. Through these studies, they have determined the optimal operating modes of the installation and identified characteristic regions of each battery type that can be automatically detected on an X-ray. One of the unique advantages of X-ray technology is its ability to see through batteries, allowing for accurate identification in cases where labels, markings, or rust may obscure the battery’s features. This is especially valuable in situations where counterfeit batteries are prevalent on the market, and the composition of the battery may not match what is indicated on the label.
Unlike human eyes or other optical systems, X-ray technology does not rely on the label or external markings to determine a battery’s composition. Instead, the recognition algorithm is able to identify the battery type based on its internal features, ensuring accurate sorting even in cases of mislabeling or counterfeit products.
The Sorting Process
There are various methods available for sorting batteries based on their internal chemical composition which allow to quickly and accurately categorize them. These methods include manual sorting, optical sorting, sorting by weight and electrical conductivity, and magnetic sorting. As there are a vast number of different types of batteries and accumulators on the market, they are classified as hazardous solid household waste due to the presence of highly toxic heavy metals such as mercury, cadmium, or lead in varying concentrations.
According to available literature, used batteries contribute up to 40% of all toxic substances present in the environment through household waste. Some batteries and accumulators also contain valuable metals like silver, nickel, cadmium, or zinc in concentrations much higher than those found in natural ores.
BATTERAY System
X-ray system for sorting of portable waste batteries and accumulators. Our product, BATTERAY system, offers several significant advantages for commercial battery processing. These include the ability to tailor the batteries feeding hopper to various sizes depending on the enterprise’s processing line throughput. We can also modify the orientation conveyor for the required number of battery types, making the system highly flexible. Additionally we have designed a special conveyor for cleaning small debris, ensuring that only clean, single batteries are scanned. This eliminates electrolyte dust, battery debris, and small tablet batteries, producing cleaner fractions of substances and improving sorting accuracy. The entire system, apart from the scanning part, can be cleaned with a high-pressure washer, ensuring that the system remains clean and efficient. It can function in extreme weather conditions, even in hot and humid countries, making it a versatile solution for battery processing.
Our X-ray technology is not limited to sorting portable batteries. As the number of electric vehicles increases, so does the production of batteries for these vehicles. Our technology simplifies the process of product quality control and makes it more reliable. Our team is committed to tackling new challenges in the production and processing of batteries, and we are confident that our innovative solutions will continue to advance the industry.
The BATTERAY system is able to sort the following battery groups:
The battery sorting process begins when the operator fills the loading hopper, and the batteries are transferred to the conveyor for the initial separation of small debris, electrolyte dust, parts of batteries, and miniature batteries. The batteries are then moved to the orientation conveyor, where they are aligned to match the conveyor movement. As the batteries pass through the detection system, they are analyzed using our X-ray technology and assigned to a specific group. Identified batteries are then sorted into appropriate containers using pneumatic injectors, while unrecognized batteries or those with damages are directed to a separate container at the end of the conveyor.
Our conveyor speed allows for a sorting process with a productivity of up to 300 kg per hour, and the purity of sorting for Alkaline/ZnC is 99.5%, meeting the requirements of recycling companies. Our wide coverage standard map includes the most popular types and sizes of batteries, making our system suitable for a broad range of applications.
Recycling has been made successful, in part, by lead-acid batteries, with over 97 percent of them being recycled in the USA today. This process is straightforward, and up to 70 percent of the battery’s weight can be reused as lead. Recycling is responsible for providing over 50 percent of the lead supply, and its primary aim is to prevent dangerous materials from ending up in landfills while also repurposing the extracted components to make new products.
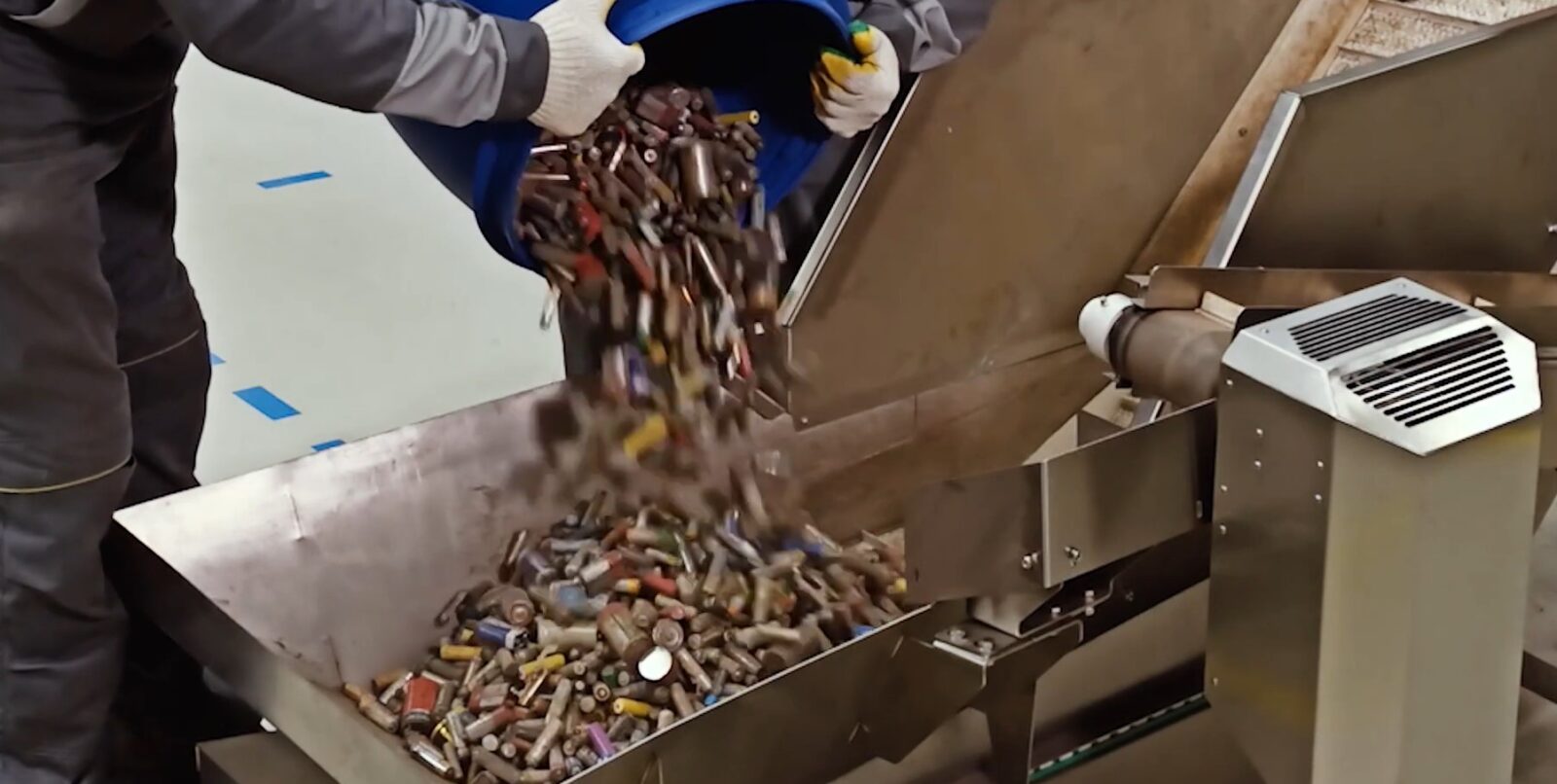
Though batteries containing harmful substances will continue to be present, using them is not an issue as long as they are properly disposed of. Each battery type necessitates a distinct recycling process, which starts by sorting them into the appropriate categories.
Certain batteries and accumulators possess high concentrations of costly metals such as silver, nickel, cadmium, or zinc that exceed those found in natural ores. The production of batteries and accumulators is on a continual rise. As a result, collecting, categorizing, and recycling these products is vital to prevent hazardous heavy metals from entering the environment through household waste. It is also sensible to use raw materials from used batteries or accumulators in the metallurgical industry.
To effectively reuse valuable metals and substances in the industry, it is crucial to have a high degree of purity in the recycled battery sample, which is ideally over 95%. This is why sorting old batteries and accumulators by their electrolyte type is necessary after they have been collected in containers. Since 2017 our team has researched the possibility of using X-ray technology to solve the problem of identifying and sorting various types of used batteries. As a result, the X-ray system for sorting portable batteries, BATTERAY, was developed and manufactured. The BATTERAY, X-Ray Battery Testing system is a powerful and versatile tool for detecting the types of batteries.
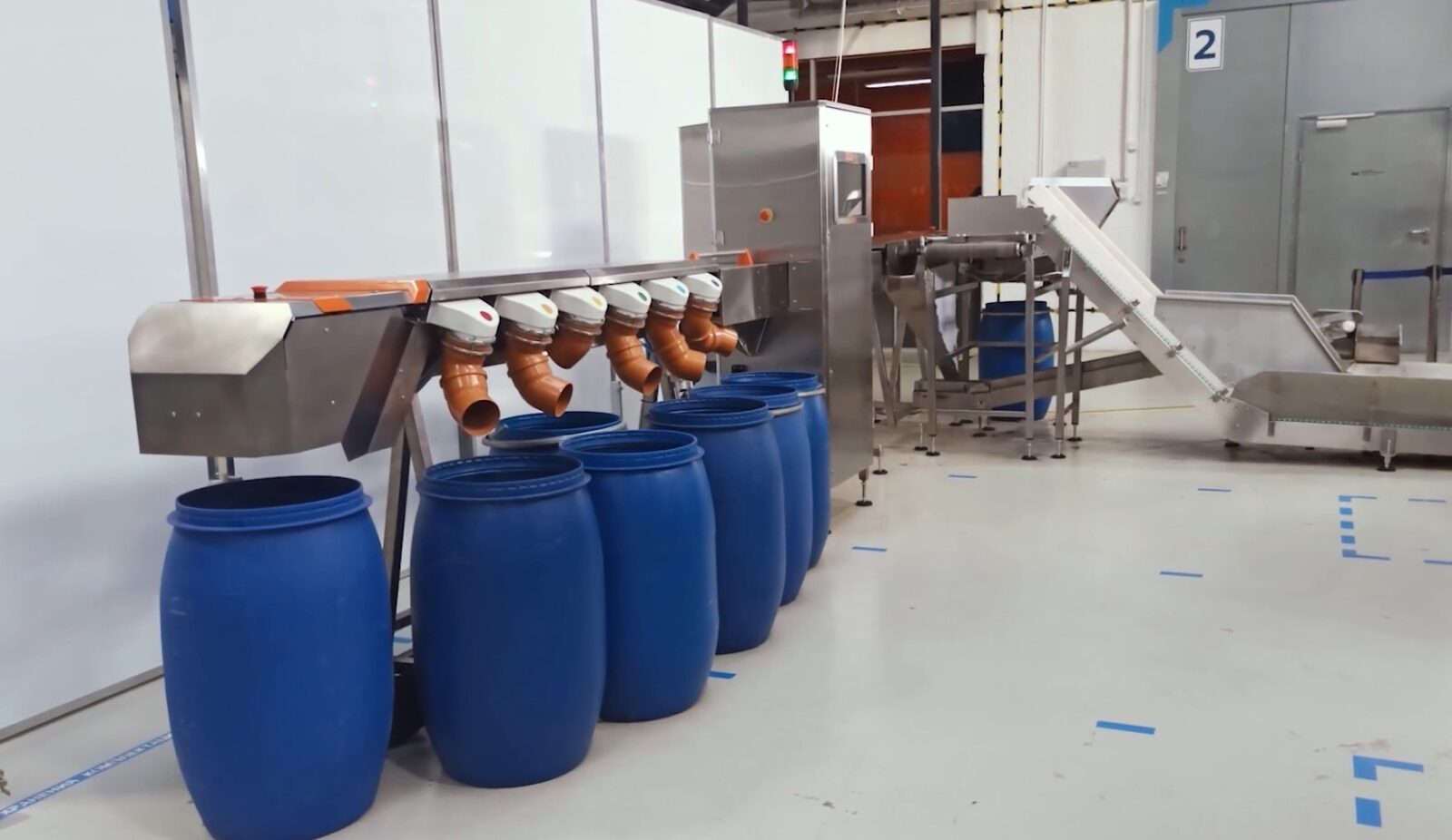
LINEV Systems Has The Solution
By implementing our technology at the sorting stage, we can increase the overall efficiency of the recycling process by increasing the number of recycled batteries and reducing the cost of recycling. This will reduce the cost of all stages of the recycling process. Furthermore, the quality of the final product of processing is directly related to the quality of sorting. Different types of batteries yield different fractions of substances with various fields of application. Heavy metals in fertilizers can defeat their agricultural purpose, while impurities in metals can make the metallurgical processing process more difficult. It is also essential to note that higher sorting purity dramatically reduces the risk of emergencies such as explosions and fires in lithium battery recycling plants.
The LINEV Group has been conducting research since 2018 to investigate the feasibility of using X-ray technology to identify and sort various types of used batteries. Through these studies, they have determined the optimal operating modes of the installation and identified characteristic regions of each battery type that can be automatically detected on an X-ray. One of the unique advantages of X-ray technology is its ability to see through batteries, allowing for accurate identification in cases where labels, markings, or rust may obscure the battery’s features. This is especially valuable in situations where counterfeit batteries are prevalent on the market, and the composition of the battery may not match what is indicated on the label.
Unlike human eyes or other optical systems, X-ray technology does not rely on the label or external markings to determine a battery’s composition. Instead, the recognition algorithm is able to identify the battery type based on its internal features, ensuring accurate sorting even in cases of mislabeling or counterfeit products.
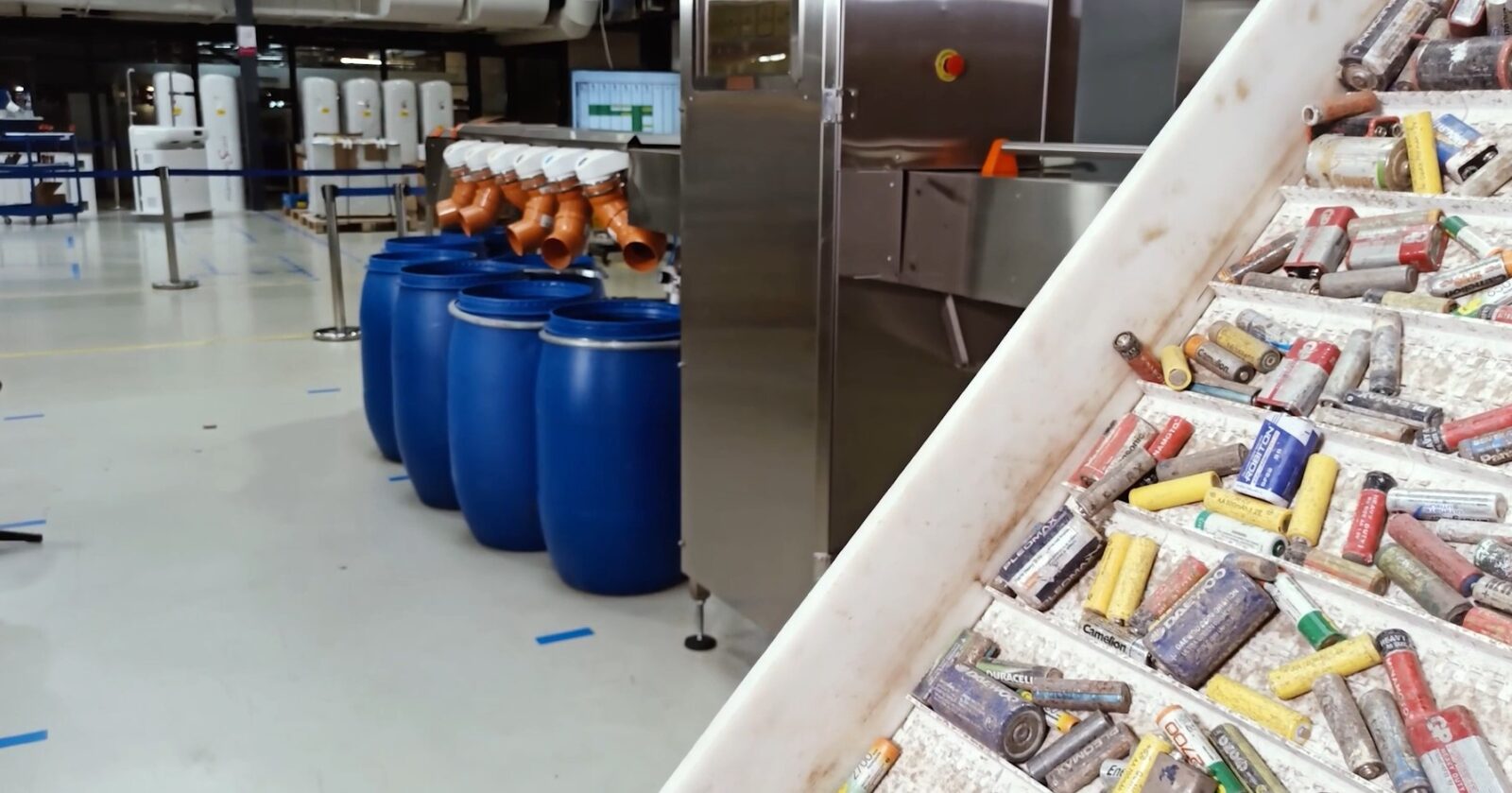
The Sorting Process
There are various methods available for sorting batteries based on their internal chemical composition which allow to quickly and accurately categorize them. These methods include manual sorting, optical sorting, sorting by weight and electrical conductivity, and magnetic sorting. As there are a vast number of different types of batteries and accumulators on the market, they are classified as hazardous solid household waste due to the presence of highly toxic heavy metals such as mercury, cadmium, or lead in varying concentrations.
According to available literature, used batteries contribute up to 40% of all toxic substances present in the environment through household waste. Some batteries and accumulators also contain valuable metals like silver, nickel, cadmium, or zinc in concentrations much higher than those found in natural ores.

BATTERAY System
X-ray system for sorting of portable waste batteries and accumulators. Our product, BATTERAY system, offers several significant advantages for commercial battery processing. These include the ability to tailor the batteries feeding hopper to various sizes depending on the enterprise’s processing line throughput. We can also modify the orientation conveyor for the required number of battery types, making the system highly flexible. Additionally we have designed a special conveyor for cleaning small debris, ensuring that only clean, single batteries are scanned. This eliminates electrolyte dust, battery debris, and small tablet batteries, producing cleaner fractions of substances and improving sorting accuracy. The entire system, apart from the scanning part, can be cleaned with a high-pressure washer, ensuring that the system remains clean and efficient. It can function in extreme weather conditions, even in hot and humid countries, making it a versatile solution for battery processing.
Our X-ray technology is not limited to sorting portable batteries. As the number of electric vehicles increases, so does the production of batteries for these vehicles. Our technology simplifies the process of product quality control and makes it more reliable. Our team is committed to tackling new challenges in the production and processing of batteries, and we are confident that our innovative solutions will continue to advance the industry.
The BATTERAY system is able to sort the following battery groups:
- Zn-Carbon
- Alkaline
- Li-Ion
- Li-Primary
- Nickel-Cadmium (NiCd)
- Nickel-Metal hydride (NiMH)
The battery sorting process begins when the operator fills the loading hopper, and the batteries are transferred to the conveyor for the initial separation of small debris, electrolyte dust, parts of batteries, and miniature batteries. The batteries are then moved to the orientation conveyor, where they are aligned to match the conveyor movement. As the batteries pass through the detection system, they are analyzed using our X-ray technology and assigned to a specific group. Identified batteries are then sorted into appropriate containers using pneumatic injectors, while unrecognized batteries or those with damages are directed to a separate container at the end of the conveyor.
Our conveyor speed allows for a sorting process with a productivity of up to 300 kg per hour, and the purity of sorting for Alkaline/ZnC is 99.5%, meeting the requirements of recycling companies. Our wide coverage standard map includes the most popular types and sizes of batteries, making our system suitable for a broad range of applications.