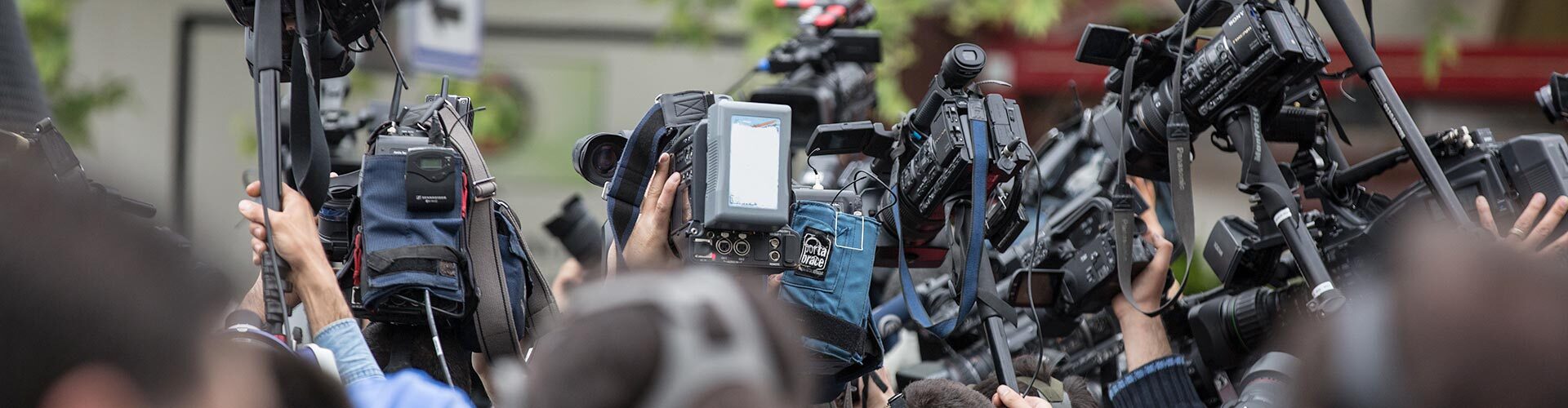
02 October 2024
Battery Sorting Technology: Innovations in Sorting, Recycling, and Disposal
LINEV Systems has been dedicated since 2017 to creating cutting-edge technologies that tackle the worldwide problem of battery recycling. The accuracy of traditional sorting systems, which depend on surface cues like form or markings, is frequently limited, particularly when handling damaged, fake, or unlabeled batteries. BATTERAY, an X-ray-based sorting system designed to effectively classify and identify a broad range of old batteries, was developed in response to this difficulty. BATTERAY is a ground-breaking technology that has the potential to revolutionize battery recycling by utilizing X-ray imaging, artificial intelligence, and accurate mechanical sorting. BATTERAY’s sophisticated X-ray imaging technology is the foundation of its operation. BATTERAY goes beyond traditional sorting methods, which mostly rely on the batteries’ outward appearance. The technology takes precise interior pictures of every battery using X-ray radiation, which allows it to identify even the smallest variations in structural arrangement and chemical makeup. This feature is especially important when labels are broken, absent, or fake, as happens frequently with used batteries. BATTERAY removes the element of guesswork by examining these internal features, offering precise classification independent of the exterior condition of the battery.
The capabilities of BATTERAY are further improved by the use of artificial intelligence. Each battery is scanned, and BATTERAY’s AI algorithms examine its internal structure before comparing it to a large library of pre-established battery types. As the system gains knowledge from new data, this database—which covers a wide variety of standard and customer-added battery types—is updated on a regular basis. Users have the option to add a new battery type to the system’s memory, enabling continuous adaption and enhancement. This procedure guarantees great accuracy, drastically lowers errors, and helps BATTERAY maintain its reputation as an almost faultless sorting tool. BATTERAY may be customized to meet a range of battery sorting requirements because to its modular design. Batteries of various chemistries, including common ones like alkaline, zinc-carbon, nickel-cadmium (NiCd), nickel-metal hydride (NiMH), primary lithium, and lithium-ion, can be accommodated by the system. Because each battery type has distinct internal characteristics that the X-ray imaging technology can identify and evaluate, BATTERAY is able to classify them with remarkably high accuracy. The system is compatible with a wide range of consumer and industrial battery types, with battery sizes ranging from AAAA to 21700. Because of its adaptability, BATTERAY can be used for a variety of tasks, such as separating specialty batteries used in electronics and industrial equipment or sorting domestic batteries for recycling.
BATTERAY’s versatility goes beyond its modular architecture. Operators can alter sorting parameters according to particular needs thanks to the system’s intuitive interface. Standard battery kinds, for instance, are included in the sort map by default, but users can optionally add non-standard sizes and chemistries as needed. For facilities that deal with a variety of battery types, this versatility is essential because it allows them to tune BATTERAY for optimal accuracy and efficiency. Its effectiveness is among BATTERAY’s most impressive qualities. The conveyor belt of the system can sort 350 to 500 kilos of batteries every hour, depending on the mix of battery types, at a speed of 1.0 meters per second. Large-scale operations where fast throughput is crucial are ideally suited for BATTERAY, which can process up to 25,000 batteries per hour. The system’s pneumatic sorting mechanism, which employs high-pressure air to drive batteries into specific compartments based on their chemistry, significantly improves this efficiency. Compared to mechanical arms or conveyor-based sorting techniques, this method not only expedites the sorting process but also reduces the need for maintenance because the pneumatic components are robust and less likely to wear out.
Comprehensive X-ray shielding is incorporated into BATTERAY to guarantee operator safety. The system emits less than 0.3 μSv at any location 10 cm from the device, which is well below authorized limits and conforms with stringent radiation emission requirements. By shielding workers from possible radiation exposure, this complete shielding enables safe, ongoing operation in industrial settings. For added security, the design incorporates automatic safety procedures that continuously check radiation levels. BATTERAY’s dedication to security is reflected in its software, which has sophisticated quality control procedures to guarantee reliable sorting. Sorting purity is regularly monitored by the system, which keeps track of variables like mistake margins and battery identification rates. BATTERAY automatically notifies operators when performance deviates from predetermined levels, allowing for prompt action to avert possible sorting problems. The software also creates a verifiable record of every batch handled by keeping thorough logs of all sorting activities. These logs are useful for performance analysis and can assist operators in recognizing patterns, resolving persistent problems, and gradually increasing the system’s efficiency. In order to maintain and support BATTERAY, telemetry services are essential. With the help of LINEV Systems’ remote monitoring features, experts may evaluate the state of the system in real time and suggest preventative maintenance. Because it allows them to fix possible problems before they have an impact on productivity, this function is especially helpful for facilities that depend on BATTERAY for continuous operation. Telemetry improves the BATTERAY system’s overall dependability by lowering downtime and the requirement for on-site service calls, guaranteeing that it stays functional and effective.
It is impossible to overestimate BATTERAY’s contribution to environmental sustainability in addition to its technical features. BATTERAY lessens the negative effects of battery waste on the environment by precisely classifying batteries for recycling or appropriate disposal. If batteries are not disposed of appropriately, they can release harmful substances including heavy metals and poisonous compounds into the ground and water. Each battery type is sent to the proper recycling procedure thanks to BATTERAY’s accurate classification, which reduces the possibility of environmental contamination. This dedication to environmentally friendly methods supports international initiatives to cut down on technological waste and save natural habitats. The problem of detecting fake batteries is also addressed by BATTERAY’s usage of AI and X-ray technologies. Because counterfeit batteries frequently have irregular internal structures or improper labeling, it can be challenging to identify them using standard sorting techniques. By seeing each battery’s internal makeup, BATTERAY can differentiate real batteries from fakes, lowering the possibility that fakes may end up in the recycling stream. This function is especially helpful in sectors like electronics production and transportation where fake batteries represent a serious safety risk.
BATTERAY’s pneumatic sorting technology is one of its greatest operational advantages. Following identification, batteries are guided to designated sections by a high-pressure air system, which offers a rapid and effective sorting method without the need of revolving blades or mechanical arms. Because pneumatic sorting removes the possibility of mechanical failure linked to moving parts, it is not only quicker but also more dependable. Although the system needs a steady flow of high-pressure air, its sturdy construction guarantees enduring operation with little upkeep.
BATTERAY can be set up to employ other sorting methods, like robotic arms or electromechanical rotators, in situations where pneumatic sorting is not practical. For some uses, such handling larger batteries or intricate battery assemblies, these alternatives provide more precision even if they could be slower than pneumatic sorting. Because of its adaptability, the system may be customized to match the particular needs of every facility, whether those needs are related to speed, accuracy, or flexibility. BATTERAY provides a set of tools to track and improve sorting performance for establishments that place a high priority on quality control. Statistical algorithms included into the program monitor operational metrics like throughput rates, sorting purity, and battery identification accuracy. These metrics give operators important information about how well the system is performing, enabling them to make data-driven choices that will increase productivity. Additionally, BATTERAY has extra sensors to identify and stop possible obstructions, guaranteeing seamless functioning and lowering the possibility of interruptions.
LINEV Systems uses remote telemetry to offer full customer assistance to its clients throughout the world. With the use of this service, the business may remotely monitor every BATTERAY system and give customers real-time updates on system performance and maintenance requirements. If there is a technical problem, LINEV’s support staff can identify and fix it remotely, reducing downtime and guaranteeing that BATTERAY keeps working. For facilities that depend on BATTERAY for ongoing sorting, this degree of assistance is especially beneficial because it preserves production and lessens the need for on-site maintenance. BATTERAY is a major breakthrough in battery sorting technology that combines X-ray imaging, AI-driven sorting, and sturdy mechanical solutions. It is a useful tool in the field of battery recycling because of its exceptional capacity to precisely identify and classify batteries without the need for extra features. BATTERAY is poised to transform battery sorting and recycling with its high throughput, safety features, and dedication to environmental sustainability, helping to create a safer and cleaner future for battery management globally.
The capabilities of BATTERAY are further improved by the use of artificial intelligence. Each battery is scanned, and BATTERAY’s AI algorithms examine its internal structure before comparing it to a large library of pre-established battery types. As the system gains knowledge from new data, this database—which covers a wide variety of standard and customer-added battery types—is updated on a regular basis. Users have the option to add a new battery type to the system’s memory, enabling continuous adaption and enhancement. This procedure guarantees great accuracy, drastically lowers errors, and helps BATTERAY maintain its reputation as an almost faultless sorting tool. BATTERAY may be customized to meet a range of battery sorting requirements because to its modular design. Batteries of various chemistries, including common ones like alkaline, zinc-carbon, nickel-cadmium (NiCd), nickel-metal hydride (NiMH), primary lithium, and lithium-ion, can be accommodated by the system. Because each battery type has distinct internal characteristics that the X-ray imaging technology can identify and evaluate, BATTERAY is able to classify them with remarkably high accuracy. The system is compatible with a wide range of consumer and industrial battery types, with battery sizes ranging from AAAA to 21700. Because of its adaptability, BATTERAY can be used for a variety of tasks, such as separating specialty batteries used in electronics and industrial equipment or sorting domestic batteries for recycling.
BATTERAY’s versatility goes beyond its modular architecture. Operators can alter sorting parameters according to particular needs thanks to the system’s intuitive interface. Standard battery kinds, for instance, are included in the sort map by default, but users can optionally add non-standard sizes and chemistries as needed. For facilities that deal with a variety of battery types, this versatility is essential because it allows them to tune BATTERAY for optimal accuracy and efficiency. Its effectiveness is among BATTERAY’s most impressive qualities. The conveyor belt of the system can sort 350 to 500 kilos of batteries every hour, depending on the mix of battery types, at a speed of 1.0 meters per second. Large-scale operations where fast throughput is crucial are ideally suited for BATTERAY, which can process up to 25,000 batteries per hour. The system’s pneumatic sorting mechanism, which employs high-pressure air to drive batteries into specific compartments based on their chemistry, significantly improves this efficiency. Compared to mechanical arms or conveyor-based sorting techniques, this method not only expedites the sorting process but also reduces the need for maintenance because the pneumatic components are robust and less likely to wear out.
Comprehensive X-ray shielding is incorporated into BATTERAY to guarantee operator safety. The system emits less than 0.3 μSv at any location 10 cm from the device, which is well below authorized limits and conforms with stringent radiation emission requirements. By shielding workers from possible radiation exposure, this complete shielding enables safe, ongoing operation in industrial settings. For added security, the design incorporates automatic safety procedures that continuously check radiation levels. BATTERAY’s dedication to security is reflected in its software, which has sophisticated quality control procedures to guarantee reliable sorting. Sorting purity is regularly monitored by the system, which keeps track of variables like mistake margins and battery identification rates. BATTERAY automatically notifies operators when performance deviates from predetermined levels, allowing for prompt action to avert possible sorting problems. The software also creates a verifiable record of every batch handled by keeping thorough logs of all sorting activities. These logs are useful for performance analysis and can assist operators in recognizing patterns, resolving persistent problems, and gradually increasing the system’s efficiency. In order to maintain and support BATTERAY, telemetry services are essential. With the help of LINEV Systems’ remote monitoring features, experts may evaluate the state of the system in real time and suggest preventative maintenance. Because it allows them to fix possible problems before they have an impact on productivity, this function is especially helpful for facilities that depend on BATTERAY for continuous operation. Telemetry improves the BATTERAY system’s overall dependability by lowering downtime and the requirement for on-site service calls, guaranteeing that it stays functional and effective.
It is impossible to overestimate BATTERAY’s contribution to environmental sustainability in addition to its technical features. BATTERAY lessens the negative effects of battery waste on the environment by precisely classifying batteries for recycling or appropriate disposal. If batteries are not disposed of appropriately, they can release harmful substances including heavy metals and poisonous compounds into the ground and water. Each battery type is sent to the proper recycling procedure thanks to BATTERAY’s accurate classification, which reduces the possibility of environmental contamination. This dedication to environmentally friendly methods supports international initiatives to cut down on technological waste and save natural habitats. The problem of detecting fake batteries is also addressed by BATTERAY’s usage of AI and X-ray technologies. Because counterfeit batteries frequently have irregular internal structures or improper labeling, it can be challenging to identify them using standard sorting techniques. By seeing each battery’s internal makeup, BATTERAY can differentiate real batteries from fakes, lowering the possibility that fakes may end up in the recycling stream. This function is especially helpful in sectors like electronics production and transportation where fake batteries represent a serious safety risk.
BATTERAY’s pneumatic sorting technology is one of its greatest operational advantages. Following identification, batteries are guided to designated sections by a high-pressure air system, which offers a rapid and effective sorting method without the need of revolving blades or mechanical arms. Because pneumatic sorting removes the possibility of mechanical failure linked to moving parts, it is not only quicker but also more dependable. Although the system needs a steady flow of high-pressure air, its sturdy construction guarantees enduring operation with little upkeep.
BATTERAY can be set up to employ other sorting methods, like robotic arms or electromechanical rotators, in situations where pneumatic sorting is not practical. For some uses, such handling larger batteries or intricate battery assemblies, these alternatives provide more precision even if they could be slower than pneumatic sorting. Because of its adaptability, the system may be customized to match the particular needs of every facility, whether those needs are related to speed, accuracy, or flexibility. BATTERAY provides a set of tools to track and improve sorting performance for establishments that place a high priority on quality control. Statistical algorithms included into the program monitor operational metrics like throughput rates, sorting purity, and battery identification accuracy. These metrics give operators important information about how well the system is performing, enabling them to make data-driven choices that will increase productivity. Additionally, BATTERAY has extra sensors to identify and stop possible obstructions, guaranteeing seamless functioning and lowering the possibility of interruptions.
LINEV Systems uses remote telemetry to offer full customer assistance to its clients throughout the world. With the use of this service, the business may remotely monitor every BATTERAY system and give customers real-time updates on system performance and maintenance requirements. If there is a technical problem, LINEV’s support staff can identify and fix it remotely, reducing downtime and guaranteeing that BATTERAY keeps working. For facilities that depend on BATTERAY for ongoing sorting, this degree of assistance is especially beneficial because it preserves production and lessens the need for on-site maintenance. BATTERAY is a major breakthrough in battery sorting technology that combines X-ray imaging, AI-driven sorting, and sturdy mechanical solutions. It is a useful tool in the field of battery recycling because of its exceptional capacity to precisely identify and classify batteries without the need for extra features. BATTERAY is poised to transform battery sorting and recycling with its high throughput, safety features, and dedication to environmental sustainability, helping to create a safer and cleaner future for battery management globally.