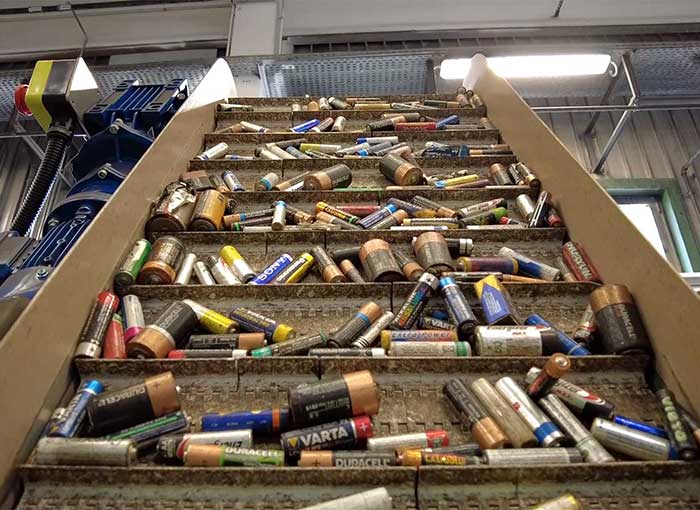
08 April 2025
Battery Recycling with LINEV’s X-ray Machine for Sorting Waste Batteries
A key component of global initiatives to reduce technological waste and move toward a more sustainable future is battery recycling. However, since broken, corroded, or counterfeit batteries pose a risk to workers, sorting and recycling batteries can be dangerous. The risks, which include fire threats and possible chemical leaks, require strict automation and safety procedures. Automation and state-of-the-art technologies like the X-ray machine for sorting waste batteries from LINEV Systems® are vital in improving worker safety and recycling efficiency.
Key Features of the BATTERAYTM X-Ray System
The Challenges of Battery Recycling
Battery recycling is not at all simple. There are several different chemistries available in batteries, including:- Zn-Carbon
- Alkaline
- Lithium-Ion (Li-Ion)
- Lithium-Primary (Li-SOCl2, Li-MnO2, Li-FeS2)
- Nickel-Cadmium (NiCd)
- Nickel-Metal Hydride (NiMH)
- Toxic Fumes: Respiratory systems can be harmed by long exposure to fumes from nickel, lithium, and cadmium.
- Thermal Fires: Lithium-ion batteries that are damaged are more likely to overheat and catch fire. Thermal fires are extremely hard to put as they can react with water.
- Chemical Burns: Workers are at risk of serious chemical burns or pollution from battery leaks.
Key Features of the BATTERAYTM X-Ray System
- Damaged Battery Detection: This technology identifies and isolates damaged, corroded, or counterfeit batteries, minimizing worker risks.
- Artificial Intelligence Integration: AI-driven sorting ensures high accuracy by distinguishing between different battery chemistries in real time.
- High Productivity: The system achieves sorting productivity of up to 350 kg per hour, surpassing manual sorting speeds while maintaining worker safety.
- Purity of Sorting: With a sorting purity of 99.5% for Alkaline/ZnC batteries and over 90% for other types, it ensures high-quality recycling outputs.
- Non-Contact Analysis: By doing away with the necessity of physically handling dangerous batteries, X-ray imaging lowers the risk of exposure to dangerous chemicals or thermal reactions.
- Real-Time Detection: Batteries that are corroded or damaged can be identified by our AI-powered X-ray machine.
- Reduced Manual Labor: By reducing the number of workers needed to sort batteries manually, automation helps to lower worker risk.
- Improved Operational Efficiency Facilities can manage higher amounts of batteries due to automated technology that speeds up sorting and processing. The BATTERAYTM X-ray system guarantees that facilities can meet increasing recycling demands with its capacity to handle 350 kg of batteries per hour.
- Minimized Risks of Workplace Accidents By automating the most dangerous parts of the sorting process, workers are less likely to get injuries from handling corroded or damaged batteries.
- Compliance with Environmental Regulations Battery management and recycling are subject to strict regulations in many nations. By precisely separating battery chemistries and isolating hazardous elements, advanced battery sorting technology guarantees compliance.
- Higher Quality Recycling Output The overall quality of recovered materials is improved by automated processes, increasing their value for reuse. For common battery types, sorting purity levels exceed 99.5%.
- Expanded AI Capabilities: The efficiency and accuracy of sorting will be further increased by improved machine learning algorithms.
- Integration with Circular Economy Models: A circular economy is facilitated by automation, which makes it possible to recover valuable elements like nickel, cobalt, and lithium.
- Increased Worker Training: Workers will require training to operate and maintain these sophisticated devices as automation becomes more common.